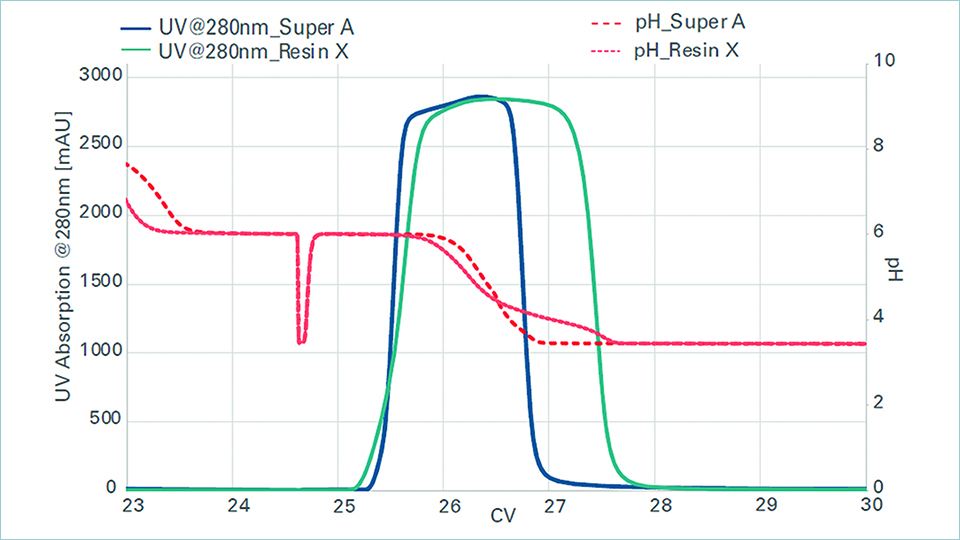
Ensuring sustainability and continuity in biomanufacturing
Biomanufacturers must balance the development of new therapeutic modalities and reduce manufacturing costs while maintaining environmental responsibility. Efforts are centred on improving process robustness and efficiency and creating more flexible manufacturing facilities that can accommodate diverse biopharmaceutical products.
The biopharmaceutical industry is entering an exciting and transformative phase. Increasing demand for treatments that address unmet medical needs while remaining affordable is driving significant changes. This is reflected in the rising number of FDA approvals for biologics each year. Biopharma manufacturers are expanding beyond monoclonal antibodies (mAbs) into new modalities, such as cell and gene therapies, without losing focus on the substantial market potential of mAbs.
Key strategies to improve development and manufacturing while aiming for sustainable operations include adopting single-use technologies, implementing process intensification and continuous manufacturing, enhancing process analytics, and developing digital capabilities to leverage AI.
Sustainable product development
At Tosoh Bioscience, we are committed to supporting biopharmaceutical manufacturers in achieving their goals of producing affordable, high-quality medicines. In addition, sustainability is a core value at Tosoh, integrated into every facet of our business. We are dedicated to implementing robust sustainability measures at the corporate level and incorporating eco-friendly practices into our product development to enable more sustainable production processes in the biopharma industry. One of the ways the industry pursues sustainability is through process intensification and continuous manufacturing. Continuous manufacturing not only enables more sustainable manufacturing but also streamlines production and enhances the flexibility and scalability of biopharmaceutical operations, allowing for faster responses to market demands and regulatory changes.
Continuous manufacturing
To simplify continuous biomanufacturing, we have developed flexible and scalable Multi Column Chromatography (MCC) skids: Octave BIO for process development and OctaveTM PRO for GMP scale production, along with SkillPakTM Prepacked Chromatography Columns. Through collaboration with Catalent Pharma/Novo, one of the largest global contract development and manufacturing organisations (CDMOs), we have optimised both the hardware and software for the Octave PRO skid to facilitate GMP operations. This partnership accelerated the implementation of multi-column chromatography (MCC) in the highly regulated clinical-materials production stage.
Partnering for future innovation
To further develop MCC instruments to anticipate future developments in the industry, we joined the ECOnti project to develop innovative technologies that enable smaller production facilities, reduce water and energy consumption, and help companies limit their CO2 emissions. This project, led by enGenes Biotech GmbH and supported by the Austrian Research Funding Agency (FFG), aims to develop a fully integrated and automated continuous upstream and downstream process at up to 10L batch size, featuring the Octave BIO MCC Skid. The technology developed within the ECOnti project offers several key advantages, including smaller production facilities, reduced water consumption, lower energy consumption and CO2 emissions, end-to-end process control, full digitisation and automation, higher product yields, and enhanced process stability.
Additionally, Tosoh Bioscience has announced a pioneering partnership with Prof D. Michael Wolff from the University of Applied Sciences Mittelhessen (THM) Gießen, Germany. This collaboration focuses on developing continuous purification processes for viruses and viral vectors. By financing a researcher position and supplying essential equipment, including an Octave BIO Multi-Column Chromatography system, Tosoh Bioscience is dedicated to advancing solutions that meet the critical needs of the cell and gene therapy (CGT) industry. This partnership exemplifies our commitment to innovation and industry-academic collaborations, aiming to make CGT manufacturing processes more cost-effective and accessible.
Single-use products
The commitment to provide advanced solutions extends to the design of single-use consumables. A first example is our SkillPak Prepacked Chromatography Columns. By 2025, we will introduce columns for GMP production, with dedicated product lines for both batch and MCC applications. They will use significantly less plastic than traditional options and incorporate recycled glass fibers, further supporting sustainable practices.
More efficient mAb manufacturing
To enhance process robustness and flexibility, our brand new TOYOPEARL® Super A resin offers significant advantages for mAb manufacturers looking to implement a capturing platform to reduce their time-to-market. This high-performance protein A resin offers industry-leading critical performance parameters along with flexible operational parameters: high binding capacity at shorter retention times, robust alkaline stability, reduced pressure loss, and minimised aggregation with elution at pH 4.0. These attributes bring more process flexibility and robustness to antibody manufacturing, improving overall efficiency and product quality. TOYOPEARL® Super A resin is the ideal choice for small and large-scale bioprocessing. Its advanced features improve process economics and ensure high-quality, safe, and effective monoclonal antibody purification.
Business continuity
Post-COVID, the emphasis on business continuity has intensified, with manufacturers forging closer collaborations with suppliers of critical consumables to ensure supply chain resilience. To bolster business continuity, we are expanding our manufacturing capacities. This includes constructing Tosoh’s fifth manufacturing facility at the Yokkaichi Complex in Yokkaichi City, Mie Prefecture. This facility complements the fourth plant currently under construction in Nanyo, Yamaguchi Prefecture, which will be operational in 2025. Our fifth site for chromatography media is tentatively expected to be operational by mid-2027. These expansions ensure that our customers can confidently plan for business continuity and have assured supply for their future expansion
needs.
Future developments
The biopharmaceutical industry is navigating a period of rapid change and growth. The drive to address unmet medical needs with new and affordable treatments pushes manufacturers to innovate and adapt. Tosoh Bioscience is committed to supporting these efforts through our capacity expansions, process intensification initiatives, and unwavering commitment to sustainability. We are also engaged in numerous promising R&D projects at various stages of development aimed at supporting customers in their process development efforts for novel modalities like Oligonucleotides, AAVs and others. We view innovation and sustainability as an ongoing journey. Our approach includes continuous improvement, investing in research and development for more efficient and sustainable products, and partnering with stakeholders. By working closely with our partners and continually investing in research and development, we strive to help the biopharmaceutical industry meet its ambitious goals and improve patient outcomes worldwide.
Author: Balu Guduri, Global Product Manager – Process Consumables, Tosoh Bioscience
This advertorial was originally published in European Biotechnology Magazine Autumn 2024.