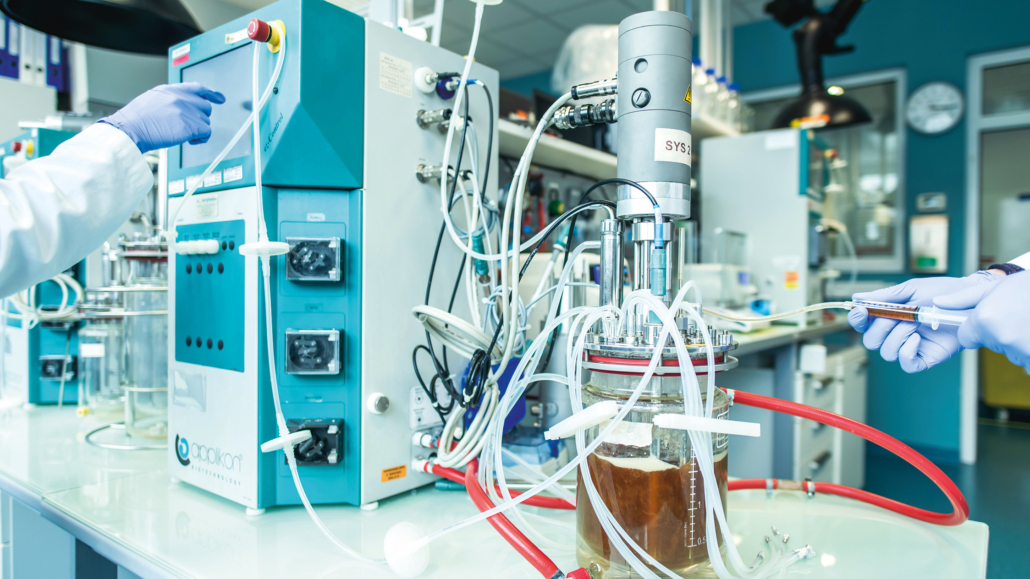
High value biopharma process development
Biomanufacturing?Implementing high-quality process development that considers GMP manufacturing from the start is critical to reducing costs and timeline disruptions associated with raw material supply chain insecurity, adhering to regulatory compliance, and avoiding process re-design at a later stage.
In overly ambitious biopharmaceutical development timelines, overlooking a GMP-suited process is common. The key milestone is producing during a pre-booked GMP slot to achieve first-to-clinical Phase I status, but manufacturing capacity is typically booked far in advance, making rescheduling difficult and costly.
Amidst the rush to meet timelines, biopharma companies and their partners often overlook crucial factors such as raw material availability and equipment compatibility. For instance, limited availability of resins may impede timely scaling up of a process, while a process designed for Phase I may lack scalability for commercial production. As an example, only a portion of USP material is utilised in Phase I’s downstream process since minimal material is needed, but a scalability issue arises when moving to commercial scale.
In some instances, biopharma companies collaborate with CROs who have different objectives, solely focused on developing the drug substance process for early-phase development, which permits sponsors to evaluate the protein’s/antibody’s mode of action in a research environment. Sponsors may be at fault for overlooking this, prioritising meeting pre-set milestones in Phases I, II, and III, while compromising on complete process development, often leading to issues like yield or purity shortcomings, or a non-scalable/non-robust process. Only after that they consider scale-up, commercialisation, and ways to increase efficiencies and reduce process costs.
Inadequate process development has severe consequences. If significant process redesign is necessary, it may require repeating toxicology and Phase I/Phase II studies, resulting in a loss of both time and money. This further shortens the commercialisation period until patent expiration, exacerbating the situation. Consequently, finding a licensing partner for commercialisation becomes challenging, even with a persuasive scientific mode of action. The cost of goods sold (COGS) for that partner, potentially during a shorter commercialisation phase due to the impending patent expiration, does not warrant the investment needed to redesign a suboptimal GMP production process.
Ultimately, high-quality process development aims to maintain consistency from toxicology through GMP production runs. Process adaptations are usually necessary for tech transfer or scale-up to achieve higher yield, greater purity, or a more stable supply chain (e.g., changing to a resin with a shorter lead time). However, significant changes invite additional regulatory scrutiny.
Engage a CDMO partner ASAP
To ensure thorough, well-considered process development, it is crucial to secure a CDMO partner as early as possible in a project. Biopharma companies often understand that their proposed process needs optimisation and seek external expertise to achieve this. The CDMO-client conversation covers various areas, such as yield and purity improvement, investment in the process, and desired outcomes. An experienced CDMO will prioritise optimising process steps that need attention. However, some companies demand running their heavily invested process exactly as designed or resist changes due to regulatory compliance concerns. Supply chain issues may arise, leading to missed GMP runs. Even if the GMP run occurs on time, issues may expose the process as unsuitable for the scale, equipment, or facility, affecting the entire process. Therefore, regardless of when the CDMO joins a project, discussing process optimisation is crucial to ensure yield and purity improvement.
Picking the right CDMO partner
A biopharma company typically knows what kind of CDMO it wants to work with and seeks out expertise and experience with a certain process or protein. However, it is unlikely that any CDMO will have experience with a client’s exact process or protein, so adaptability and capability in handling diverse molecules are essential. Northway Biotech stands out in this regard, with experience not only in monoclonal antibodies but also bispecific and trispecific antibodies, as well as microbially produced recombinant proteins, which have different purification requirements. This expertise allows for the development of optimised processes, overcoming specific problems, and is facilitated by in-house knowledge of equipment limitations, supply chain, and facility, ensuring a suitable process for GMP-scale production.
Do not underestimate the importance of process development. A process that works in the early stages may not respond well to GMP manufacturing and scale-up, leading to additional costs and time loss. Process development is crucial not only for on-time GMP production but also for presenting a complete package to potential partners or acquirers. For more information, contact the authors and visit www.northwaybiotech.com.
This article was originally published in European Biotechnology Magazine Spring Edition 2023.