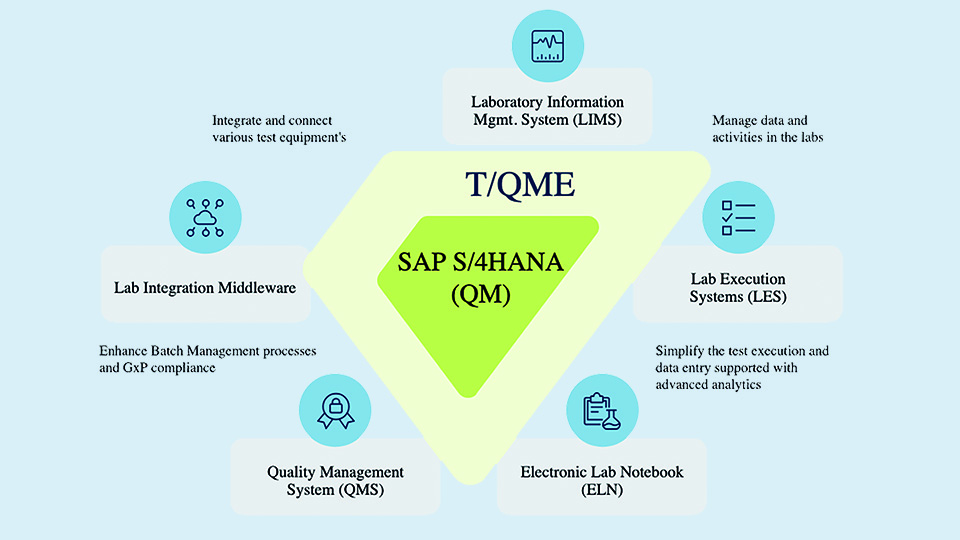
Closing the gap in Quality Management
In the life sciences industry, Quality Management (QM) has long been synonymous with compliance: checking boxes to meet regulatory demands. But that definition no longer holds up. Today, QM must do much more than ensure compliance; it needs to enable speed, scalability, and sustained innovation across complex, global operations. To do that, prominent gaps need to be filled.
Life sciences companies are currently facing a growing list of pressures and challenges that are redefining the role of quality. This includes heightened compliance requirements and more frequent audits that are placing new demands on quality systems; fragmented data sources and non-harmonised processes that make it difficult to ensure consistent quality across regions or business units; transitioning from legacy or paper-based systems to modern digital platforms; and talent shortages in quality and compliance roles. It’s a lot.
Sector-specific pressures are adding complexity. For example, in the pharmaceuticals sector, companies face tighter batch release controls, greater traceability demands, and diverging global regulatory standards. In medtech, the integration of device software and artificial intelligence (AI) introduces new validation and post-market surveillance requirements.
Current market gaps
There are several critical gaps in today’s QM systems, thanks to insights gathered in collaboration with Tenthpin’s customers’ projects. These gaps can be allocated into two types; functional and technological.
Functional gaps include the likes of certificate handling, system integration, audit, and supplier management, as well as risk management. Verification of inbound certificates and generation of outbound certificates remains largely manual or disconnected. There are still gaps between supply chain, manufacturing, and quality systems, limiting end-to-end traceability and response. Many solutions lack robust tools for audit preparation, supplier quality monitoring, and non-conformance tracking. Plus, few systems offer deeply embedded risk management features that can guide real-time decision-making. Technology gaps are also persistent. For example, AI tools, while increasingly available, remain difficult to validate and deploy in GxP-regulated environments. Smart automation is limited due to the essential need for human oversight in high-risk quality processes. There are still few truly interoperable platforms that offer an end-to-end view of quality across the enterprise. These gaps impact both operational efficiency and the ability to maintain compliance at scale. They need to be closed, but how?
QM solutions are within reach
The answer is the range of Quality Management solutions designed to meet different needs across the value chain. Enterprise Quality Management System (QMS) platforms remain a popular choice due to their configurability and scalability. Platforms that offer a wide range of capabilities, from document control and training management to deviation tracking and CAPA workflows. But the trade-off for customisation is complexity, which can impact heavily-regulated industries like life sciences.
ERP-integrated QM modules present a streamlined alternative. By embedding quality processes within the same ecosystem as finance, procurement, and supply chain operations, these modules facilitate data flow and reduce duplication of effort. However, they may lack the depth and flexibility required for complex quality workflows.
LIMS and workflows
Laboratory Information Management Systems (LIMS) also play a prominent role for companies with heavy lab-based testing and sample management requirements. While LIMS solutions excel at managing test data and ensuring traceability at the sample level, they are not designed to handle broader quality system functions, such as supplier management or complaint handling. Custom-built tools and workflows have emerged as a practical solution for many companies, especially those with unique business processes or legacy constraints. These solutions are often developed in-house or co-created with partners to address specific gaps that off-the-shelf platforms cannot cover. But which approach is the right one?
Lessons from the experts
To overcome the challenges in quality management (QM), the top 20 life sciences companies are deploying winnable strategies that are worth paying attention to.
One common trend among industry leaders is the move toward standardised, global platforms. By consolidating disparate systems and processes into unified solutions, life sciences companies are improving data consistency, enhancing traceability, and reducing the operational burden of maintaining multiple compliance frameworks. This standardisation also enables more effective governance, allowing organisations to monitor quality performance with greater clarity.
A stronger emphasis on strategic partnerships is proving to be a critical development. Leading firms are co-innovating with technology vendors and consulting partners to create solutions tailored to industry-specific needs while remaining scalable and compliant. These collaborations bring fruitful results with accelerators or industry templates that reduce implementation time and validation effort. Increasing their focus on establishing robust governance models is also a key trend. This includes clearly defined roles and responsibilities, integrated risk management practices, and performance monitoring mechanisms to ensure quality is maintained and continuously improved. By embedding quality into business planning and decision-making processes, they are making it an enabler of growth rather than a bottleneck.But not everyone is a top 20 company. So, what can smaller life sciences companies learn from it? By adopting pre-validated solutions and industry-standard frameworks, smaller firms can reduce implementation risk and accelerate time-to-value. Using proven technologies and best practices means they don’t have to start from scratch – many of the tools and insights developed by larger players can be adapted and scaled down effectively.
Ready for tomorrow?
Gaps remain in Quality Management; manual processes, outdated legacy systems, AI deployment in GxP environments, and talent shortages. But life sciences companies that make thoughtful, strategic investments in scalable, compliant, and digital-ready QM frameworks will be best positioned to navigate future complexity. At Tenthpin, we’re addressing the challenges with co-innovations like SAP Batch Release Hub (BRH) and our own solutions within the Tenthpin Intelligent Quality Suite, including Tenthpin Quality Management Evolved. Right now, 16 of the top 20 life sciences companies trust our expertise. You can too. Explore Tenthpin’s industry standard solutions to see how we help close the Quality Management gaps and future-proof your approach.
This article from Oliver Nürnberg, Director Product Management, Tenthpin Solutions AG, was originally published in European Biotechnology Magazine Summer 2025.