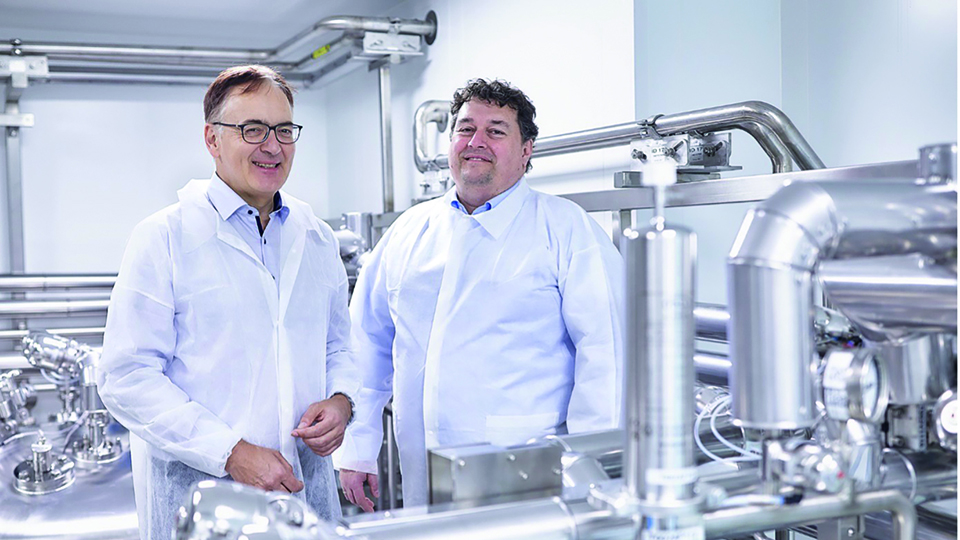
Well Prepared to Tackle New Pandemics
If you want to successfully guard against future pandemics, you’re going to need a good plan – and the right kind of vaccine producers. WACKER and CordenPharma have been commissioned by the German government to prepare their mRNA vaccine production lines for a new pandemic.
It pays to play safe. The Covid pandemic made that pretty clear. Better to be safe than sorry. A great many people took this advice to heart. Everyone was able to do something to stop the spread of the virus – such as wear a mask, keep their distance, or get tested. But the pandemic only became manageable once Covid vaccines – which were developed in record time – were made available, preventing further death and suffering. Innovative vaccines based on mRNA (messenger RiboNucleic Acid), in particular, were in high demand at the start. “The experience with scarce vaccines led to the German government’s decision secure production at home, so to speak,” explains Dr. Andreas Anton, head of Wacker Biotech’s pandemic-preparedness project in Halle (Saale). Pharmaceutical producers with appropriate vaccine expertise and capacity were then invited to apply for pandemic-preparedness contracts. Having joined forces with CordenPharma, we did precisely that, because in combination, we cover the entire process chain for producing mRNA vaccines. Alongside four other companies, we were awarded a contract in April 2022.”
That was the go-ahead for these companies to start taking all the necessary steps to achieve pandemic preparedness. In particular, the managers that WACKER and CordenPharma put in charge of the project now faced a herculean task involving an ambitious schedule: both companies needed to create the relevant setup and capacities in just two years. “In the event of a new pandemic, with Germany needing huge amounts of a particular vaccine for its population, the government would put our two companies in contact with the company that had developed the mRNA vaccine in question,” explains Dr. Alexander Radspieler, CordenPharma’s Global Project Manager, whose coordinating role is similar to that of his WACKER counterpart. CordenPharma has in-depth expertise in lipids and lipid nanoparticles and has many years of experience in terminal and aseptic filling. Wacker Biotech has become a specialist in therapeutic proteins, living biotherapeutic products, plasmid DNA and conventional vaccines based on microbial systems. It was one of the first companies to address the production of mRNA vaccines. Both companies jointly take on the vaccine’s complete production: from the bioengineering of the mRNA, starting out from plasmid DNA, through to formulation with lipid nanoparticles and the sterile filling of the final vaccine (see chart). “All the critical manufacturing steps must take place in Germany. That was specified by the German government to ensure the country’s vaccine supply. Equally, all the production steps must take place in the European Union,” explains Radspieler. “The idea is to stop being dependent on global supply chains. The importance of being independent in this respect was made patently clear by the Covid pandemic.”
This was the reason for Wacker Biotech’s choosing the site in Halle, Germany. A major expansion project was taking place at Halle’s Weinberg Campus Technology Park. CordenPharma decided to obtain pandemic-preparedness status for its production sites in Frankfurt am Main (Germany), Chenôve (France) and Caponago (Italy). All these sites were required to provide suitable production capacity by Q2 2024 to enable the annual production of 80 million vaccine units. “To meet this target, we mainly invested in Halle,” says Anton, who coordinates this large-scale project. “We have drawn up extensive schedules and project plans to achieve everything by the two-year deadline. After all, it was necessary to plan and erect a new building, obtain the requisite equipment, and take on and train considerably more staff.”
Bodyguards for the mRNA Active Ingredient
As the central process steps take place in Halle, the site plays a key part in the pandemic project. “Put simply, the first thing we do there is to use the pharmaceutical company’s specifications to make the plasmid DNA. That is the starting material for producing the mRNA active ingredient,” explains Anton. CordenPharma’s expert Radspieler adds: “The next stage involves our various lipids, as the vaccine is formulated in Halle, too. This is almost the last process stage, in which the mRNA is combined with lipids to form lipid nanoparticles, or LNPs, and packed into a lipid envelope that protects the sensitive vaccine on its way into the muscle cells at the injection point. But first, the frozen vaccine is sent to our sterile filling center in Caponago, northern Italy, where the vaccine is put in prefilled syringes or vials.” As part of measures to combat pandemics, CordenPharma launched two major expansion projects. In one project, the size of the lipid production area was increased to make it possible to produce the necessary quantities. This project also involved investing in supercritical liquid chromatography, which is an environmentally compatible purification strategy for lipids. In the other project, CordenPharma extended its existing sterile filling capacity so that it would be able to supply clinics, vaccination centers and doctor’s surgeries with the necessary vaccine doses.
After being successfully qualified and confirmed by the German government, WACKER and CordenPharma have been in a state of pandemic-readiness since June 1, 2024. To make it possible for mRNA vaccines to be produced in huge quantities, if need be, the new building in Halle includes four production lines for biopharmaceuticals – thus quadrupling Wacker Biotech’s capacity. Anton, as project manager, and his team have everything under control there: time management, adjustment of schedules, coordination of, and communication with, partners, service providers and Germany’s Center for Pandemic Vaccines and Therapeutics (ZEPAI). On 1 October 2021, the German Federal Ministry of Health (BMG) established ZEPAI at the Paul-Ehrlich-Institut (PEI) in an effort to better manage pandemic response in the field of medicinal products by establishing a framework for making pandemic vaccines available as fast as possible. Anton and Radspieler ensure that everything is good to go – first and foremost the necessary state-of-the-art equipment for bioprocess engineering. “As we don’t know the name of the customer who will be approaching us with his vaccine on day X, we basically need to be prepared for everything,” explains Anton. “When we built the new facility, we adopted a modern model process and planned for as much flexibility as possible.”
Flexibility for Production Lines
Luckily, WACKER and CordenPharma are used to rapidly switching from one customer project to another: both are CDMOs, or contract development manufacturing organizations, so it’s standard procedure for them to switch to different production processes quickly and adeptly. “As CDMOs, we make our production lines available to a wide variety of customers from the chemical and pharmaceutical sectors so that their complex modalities can be manufactured, with WACKER taking on this role for biotech firms,” explains Radspieler. “Alongside our production sites, we provide additional customer support in the form of our many years of in-depth experience. We also make our expertise relating to process management and process engineering available.”
To ensure maximum flexibility, WACKER relies on what is known as the ballroom concept in Halle. “This means that there are no permanent piping systems in our production facilities. Everything is designed to be as variable and modular as possible. It’s particularly easy to move equipment in or out of rooms. We are trying to represent a cross-section of technologies that are highly likely to be needed.” Wacker Biotech and CordenPharma have likewise adopted the notion of ‘warm base’: production facilities and staff can be deployed instantly. The necessary starting and auxiliary materials are on hand as well. The inter-site logistics strategies, too, can be implemented immediately. “If the German government gives the order to produce mRNA vaccines, we switch over to pandemic mode and can start the production process shortly after,” explains the WACKER expert. “The strategy put into effect here is one of permanent pandemic preparedness, which also benefits our customers. This makes us very flexible, enabling us, during normal customer business, to implement projects rapidly and with a high degree of supply security.”
So as not to run the risk of delays, both companies need sophisticated HR strategies, production planning and stockkeeping. Radspieler explains the reasons why: “During non-pandemic periods, our facilities are busy dealing with customer projects. As a result, we always keep production areas available for standby capacity, just like Wacker Biotech does. Or we can switch to other sites in the case of established customers – as would be the case with us when it comes to lipid production. This means that we must plan in great detail to avoid bottlenecks elsewhere,” explains Radspieler. Anton adds: “We use at least 50 percent of our capacity for customer projects, while the other half is reserved as standby capacity for vaccine production. The German government pays us compensation for doing so. Our production sites need a good mix of projects that make it easier for us to move something from A to B. For this reason, we are setting up redundant production lines.” Stockkeeping is of equal importance for the pandemic project: all the raw materials required, such as chemicals, enzymes and single-use systems, i.e. filters or plastic bags, must be present. “That’s why we designed a special storage and monitoring system so that stocks can always be kept fresh, so to speak”, explains Anton.
Both WACKER and CordenPharma profit from the fact that they were directly involved with their own projects at the start of mRNA vaccine development, which allowed them to gain experience. “For instance, our expertise meant that we were the ones that produced the lipids for the Moderna vaccine. These lipids relate, on the one hand, to cholesterol and phospholipid – two standard products – and on the other hand, to two specialty lipids that Moderna developed,” says Radspieler. “The LNPs are important for mRNA vaccines in two respects: first, as a protective envelope, second, to enable bioavailability,” explains the CordenPharma expert. During the Covid pandemic, Wacker Biotech successfully produced a clinical mRNA candidate vaccine, thereby gathering invaluable experience. The process technology needed for industrial-scale mRNA vaccine production was scaled up at WACKER’s Amsterdam site and laid the groundwork – not only in terms of the pandemic-preparedness plan, but also as regards setting up the mRNA competence center in Halle. WACKER invested more than 100 million euros in this expansion project. Over the coming years, the Group intends to spend an annual average of some 80 million euros on its biotech operations. This is yet more proof of WACKER’s confidence in this future technology.
Successful Recruitment
“To join the top league, we had to take on a lot of staff in a very short period of time and we put a great deal of effort into recruiting highly talented personnel. As we cover the entire value-creation chain, we need to recruit employees from different disciplines such as chemical and pharmaceutical technicians, IT specialists and quality managers,” says Anton. “We’ve been very successful here so far, thanks to an advertising campaign featuring influencer videos to target young people as well. It took us just one year to recruit more than 100 people,” he recounts proudly. An equally state-of-the-art approach was adopted when it came to familiarizing new staff. “On the one hand, we involved new employees in ongoing production at other corporate units. On the other, we set up dedicated training rooms so that new staff members could learn how to operate the various pieces of equipment needed for their work. If a particular piece of equipment wasn’t yet physically available, we used virtual reality modules to make the most of the familiarization phase,” explains Anton.
It’s All About Well-Laid Plans
The experts from Wacker Biotech and CordenPharma repeatedly stress that a huge number of aspects need to be taken into consideration. Pandemic preparedness depends on well-laid plans – and it’s essential to be in close contact with all the various parties involved in the project. After all, you want to play safe in the event of a new pandemic.
This advertorial was originally published in European Biotechnology Magazine Autumn 2024.