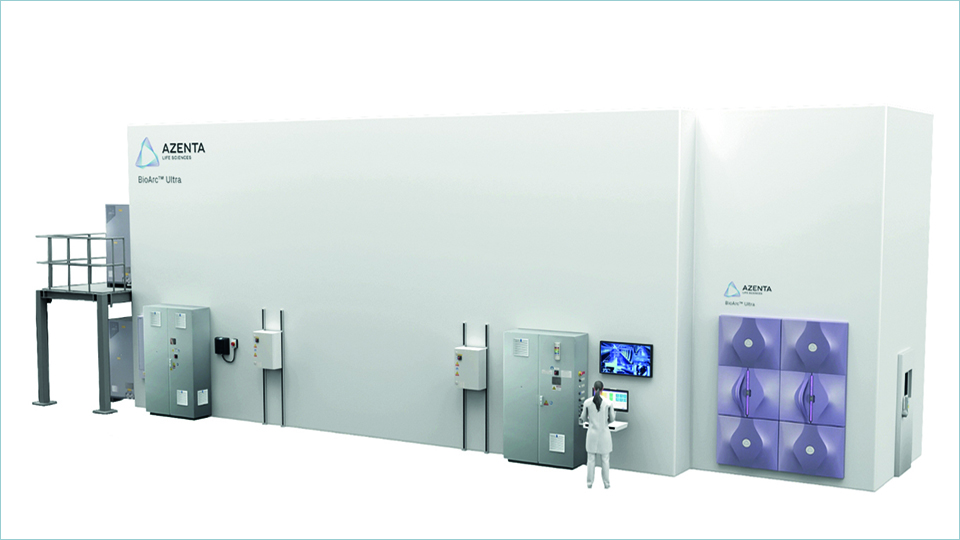
Sustainable, automated, ULT storage
The volume of samples and drug products requiring -80°C storage continues to increase, and shows no sign of slowing down. For many organisations, meeting these growing ULT storage requirements is challenging. The sheer volume of samples necessitates extensive storage capacity, which demands significant space, substantial energy use, and intensive management. Centralising and automating sample storage can provide a comprehensive solution.
Manual freezers have long been the backbone of ULT storage. While they will continue to have a crucial role in biobanking and drug development, relying on large numbers of manual freezers in “freezer farms” can have drawbacks – from labor-intensive management and inefficient space use to high running costs and environmental impact. And these limitations only become more apparent as storage needs grow.
ULT storage constraints
Freezer farms quickly consume available space, limiting the ability to store additional samples and drug products, which can ultimately hinder the expansion of research and development efforts. Moreover, sample retrieval can be slow and cumbersome, especially if freezers are spread out across a facility, which can lead to delays and increase project timelines. Sustainability concerns further complicate the picture. Many manual freezers in these farms require refrigerants with high global warming potential (GWP), consume a lot of energy and generate considerable heat. This not only increases running costs but also expands an organisation’s carbon footprint, making it more challenging to meet sustainability targets.
Centralised, automated storage
Centralising and automating ULT storage overcomes these challenges. By consolidating samples into a single, high-density automated system, organisations can better utilise space, giving them more scope to expand and future-proof their ULT storage capacity. Furthermore, these systems are often more energy-efficient, while ensuring consistent temperature control and delivering full traceability.
The BioArc™ Ultra System
The BioArc Ultra High Density -80°C Automated Sample Storage System meets the increasing demands for efficient and environmentally friendly, large-volume ULT storage.
Optimised space utilisation: With the BioArc Ultra, organisations can make better use of their available space. The system requires up to 73% less floor space than equivalent manual freezers and can accommodate up to approximately 17 million 0.9 mL tubes, offering unparalleled storage density.
Energy savings: The BioArc Ultra operates with up to 77% less power compared to equivalent manual freezers, helping to lower operational costs and reduce the total environmental impact of ULT storage.
Zero GWP: By using natural air for cooling and eliminating the use of harmful refrigerants, the BioArc Ultra achieves zero GWP, helping meet sustainability goals.
Improved efficiencies: The system automates sample management, making retrieval faster and more efficient. Additionally, Azenta’s informatics solutions ensure that customers can efficiently access and track samples during storage and retrieval, reducing the risk of human error.
Contact:
Azenta
Im Leuschnerpark 1b
64347 Griesheim, Germany
Tel: +49-6155-898-1018
https://www.azenta.com/
This advertorial was originally published in European Biotechnology Magazine Autumn 2024.