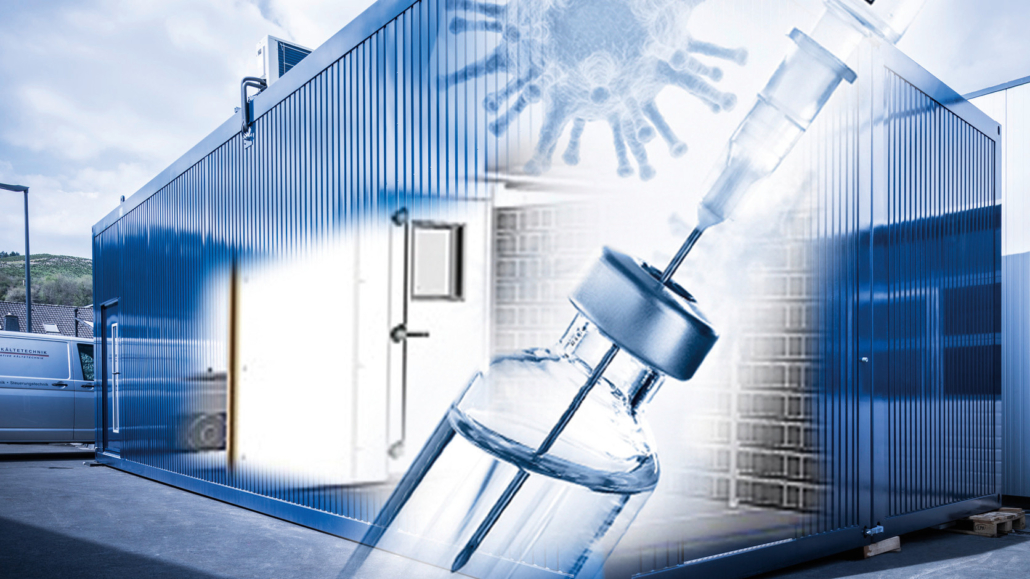
A very “cool” topic in the parmaceutical industry
The current debates regarding vaccine production and logistics have also made it clear even to the layman: Pharmaceutical production depends on cold. Temperatures below -80?°C are just as common as the requirement to freeze precursors such as blood plasma within a specified time period. Refrigeration specialists with pharmaceutical know-how are in demand for these challenging tasks.
Absolutely reliable provision of ultra-low temperatures: This is a requirement in many pharmaceutical production plants. Cooling systems installed in large production sites can reach a cooling capacity in the megawatt range and are 100% fail-safe thanks to redundant refrigerating circuits.
A current trend in the sensitive task of supplying process media and energy is the desire for high energy efficiency, which can be met by advanced drives and control systems, among other things. Equally important is the use of high quality components (pumps, heat exchangers, etc.) with very high efficiency. Central energy consumers such as compressors and pumps can either be speed-controlled or divided into several circuits to be switched on and off in a staggered manner.
The effects of the EU-wide F-Gas Regulation, which calls for a gradual phase-down of the refrigerants used to date, are still a hot topic and the subject of much discussion. Companies in the pharmaceutical industry are pursuing various strategies for the use of future-proof and environmentally friendly refrigerants. Some use new refrigerants such as HFO blends, while others basically rely on natural refrigerants such as propane, propene, CO2 or ammonia.
New concepts for cooling
As an alternative to "classic" product cooling in an ultra-low temperature environment, contact cooling is gaining acceptance in some areas of application, enabling faster and more precise freezing times. A typical example is the freezing of blood plasma in bags. Another trend is the replacement of deep freezers with walk-in deep freeze storage. Vaccine serums, stem cells, bone marrow and biomedical materials can be stored in them at temperatures typically ranging from 20°C to 80°C. Depending on each case, this solution achieves its economic break-even point when more than 10 to 15 of the usual deep freezers would otherwise have to be used.
L&R Kältetechnik (www.lr-kaelte.de) has been implementing all of these concepts for and with companies in the pharmaceutical industry for many years now. Based on this industry-specific know-how in refrigeration technology, an innovative system concept has recently been developed that specifically addresses vaccine logistics. The basic idea: A well-insulated storage cell of 20°C to 80°C with an anteroom temperature of 10°C to 20°C is installed in an industrial container with corresponding redundant, multi-stage refrigeration technology in order to guarantee a suitable (and mobile) pharmaceutical storage option for millions of doses of vaccine.
Two highly efficient, redundant refrigeration systems are installed in the 20′ or 40′ containers. The interior equipment of the GMP-compliant facility is adapted to user requirements. And if the vaccine supply should be completed at the current location, the containers can fulfil the same or a different task at another location. The operator thus benefits from both a useful and sustainable long-term investment.