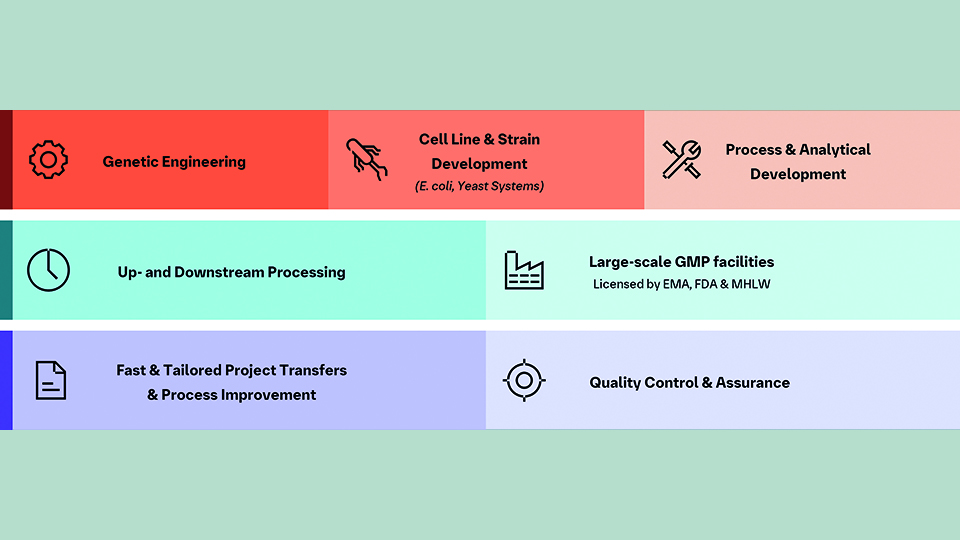
Experts in microbial technology
The world of microbial product manufacturing is a complex landscape, driven by a diverse range of molecule formats and manufacturing processes. At the forefront of this specialty market is Boehringer Ingelheim Vienna, one global leader in biopharmaceutical development and manufacturing.
With over 40 years of experience, Boehringer Ingelheim Vienna has developed and manufactured more than 150 molecules using mainly E. coli and yeast systems. These molecules range from recombinant proteins and peptides to antibody-like molecules, sub-unit vaccines, virus-like particles, and plasmid DNA. This extensive experience, combined with their broad commercial expertise and development capabilities, allows them to offer a comprehensive value chain from early-stage development to commercial launch.
Boehringer Ingelheim Vienna operates three facilities, offering flexibility with cGMP scales ranging from 300 L to 6,000 L. These multi-licensed facilities, designed for high cell density processes, have a strong manufacturing track record with 19 commercial products for global markets.
Their downstream capabilities handle a great variety of molecule formats mainly manufactured in E. coli and yeast systems. They are built on their long standing experience in protein refolding as well as soluble expression and purification at large scale, also including special techniques for difficult to manufacture proteins. To cater to these requirements facilities allow for handling organic solvents, HPLC chromatography is also available on large scale via commercial scale columns up to 1.8 m diameter and lyophilisation of bulk material is an established process step. In addition, chemical modification strategies can be applied to prolong the protein´s half-life. Among the approaches used by the company are strategies to increase size by the chemical coupling of polymers (PEGylation or HESylation) and the use of FcRn mediated recycling, such as fusion to human serum albumin (HSA) or albumin-binding moieties. Generally speaking, microbial expression systems are most suitable for synthesis of smaller and non-glycosylated proteins, whereas larger proteins like monoclonal antibodies require mammalian cell culture to be expressed. Due to the short doubling time (minutes instead of hours) microorganisms-based upstream processes are significantly (up to 30-fold) shorter than mammalian processes and yield high product titers up to 20 g/L fermentation broth.
Besides recombinant proteins, plasmid DNA for gene therapy and viral vectors can also be manufactured in E. coli. Boehringer Ingelheim has developed and continually fine-tuned a manufacturing process specifically designed to yield high-quality plasmid DNA. This process leverages the potential of scientific breakthroughs for patients.
A wide variety of molecule formats can be produced via fast cultivation in microbial systems, which present their own challenges. They require tailor-made processes, which Boehringer Ingelheim Vienna addresses with platform-like technology modules and a versatile toolbox to serve individual needs.
Microbial Process Development
Microbial systems, like Escherichia coli and Komagataella phaffii, are used to produce various proteins. The proteins can accumulate in different forms, requiring specific expression, purification, and sometimes refolding processes to reveal the proteins native and active state. These steps can be time-consuming, potentially limit throughput and may result in product losses. Regardless of the expression strategy, the need for a custom purification process adds complexity to process development and manufacturing in multi-product facilities. Technologies that simplify processes by introducing platform-like steps are beneficial for streamlining development and manufacturing, and for increasing productivity.
Fusion protein technologies, for instance, are extensively utilised to enable soluble expression and subsequent affinity purification in E. coli. However, they present several challenges, such as a reduction in product yield due to the relatively high molecular masses of tags or, more critically for biopharmaceutical applications, conformational changes that could compromise the efficacy and safety of the therapeutic protein. Boehringer Ingelheim has explored an N-terminal fusion tag, demonstrating its applicability across a broad range of molecules.
The so-called CASPON (CASPase-based fusiON) system, in particular, features a peptide fused to the N-terminus of the protein of interest and a highly specific protease to remove the tag post-purification, thereby preserving the authentic N-terminus of the target protein. Among other benefits, the tag incorporates a histidine stretch for platform affinity purification.
This exemplifies how platform-like techniques can be effectively used to mimic platform processes that are well-established for purification in cell culture manufacturing.
After defining the molecule format, a number of genetic tools can be utiliszed to boost the productivity of microbial systems. Boehringer Ingelheim has created a comprehensive toolbox, including strains, plasmids, promotors, leader sequences, and helper factors, which have been effectively used to increase soluble expression in E. coli by over 25 times.
The full potential of this multifaceted set of tools can only be harnessed with a predictive screening system. However, conventional screening systems using deep well plates or shake flask cultures often fail to accurately predict results for large scale high cell density fermentations, particularly for E. coli. To resolve this, Boehringer Ingelheim has engineered a miniaturiszed fermentation system on a milliliter scale that facilitates predictive screening of different constructs in an automated, parallel fashion. This system, coupled with miniaturised, parallelised, and automated screening systems for purification and analytics, paves the way for high throughput process development.
A predictive system is crucial for selecting the most productive strains and for the development of robust processes, which can then be scaled up and transferred. Boehringer Ingelheim employs tools such as computational fluidic dynamics (CFD) to characterise vessels of different scales and adjust small scale equipment to closely mimic the large-scale production environment.
Digital Tools for process boost
Digital tools hold considerable potential to further enhance the development and manufacturing of biopharmaceuticals. The process of developing a biopharmaceutical production process is typically sequential, and optimising each individual unit operation can be quite laborious. In this process, the conditions deemed optimal for one step serve as the basis for the next. However, this approach does not take into account potential interactions between a priori distant process steps, and therefore, cannot ensure optimal overall process performance. Data-driven integrated process models that employ machine learning techniques and genetic algorithms are powerful tools for simulating and optimising manufacturing processes. The company’s SMART Process Design software platform predicts how to adjust process parameters for optimal output. The result of this approach is a manufacturing process that provides efficiency, quality, and speed for the desired molecules, applicable to both clinical development and market supplies.
Summary
Microbial Manufacturing Technologies and Boehringer Ingelheim’s capabilities in this field offer a powerful means to produce a diverse array of products. Platform-like technologies for non-platform molecules can significantly enhance the use of microbial hosts. Digital tools for characterisation and prediction minimise the needs for wet-lab experiments and contribute significantly to the development of robust, well-understood processes. This guarantees a speed-up of time to clinic and market, ensuring patients’ access to innovative medicines.
Contact:
Dr. Rebekka Wuester
BioXcellence Contract
Manufacturing Business
Boehringer Ingelheim
Biopharmaceuticals GmbH
phone: +49 (6132) 77-0
bioxcellence@boehringer-ingelheim.com
www.bioxcellence.com