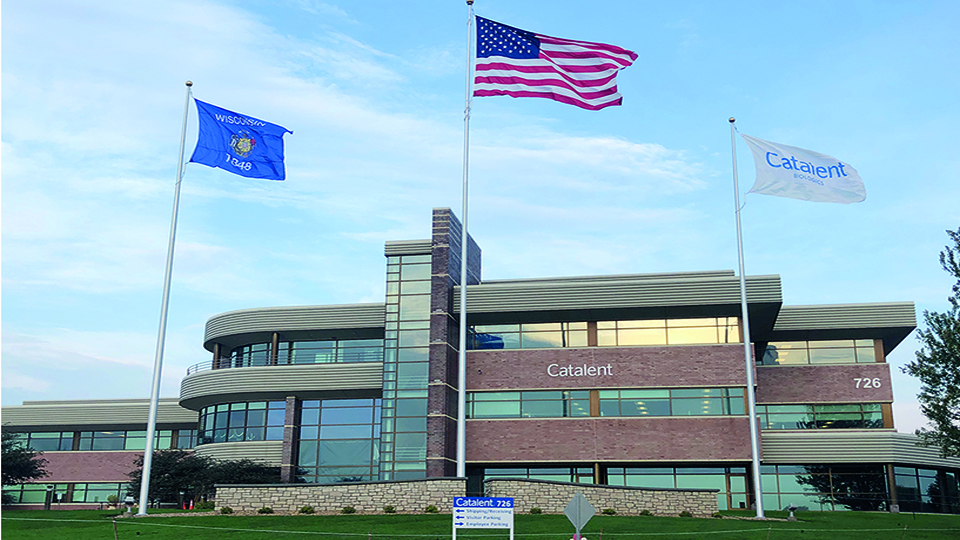
Biopharma partnership intensifying purification
DSP?Tosoh Bioscience recently launched Octave© BIO, the first in a series of MCC instruments
targeting all stages of biomolecule manufacturing. Here, Tosoh discusses the potential of MCC to help alleviate downstream bottlenecks and a process intensification collaboration they recently performed with Catalent Biologics. Emily Schirmer, Interim General Manager at Catalent Biologics, provides selected insights on Catalent's findings from the collaboration.
With broad expertise in development sciences, delivery technologies, and manufacturing, Catalent is a reliable drug development and delivery partner for the industry. In an ongoing approach to increase the efficiency of manufacturing processes, scientists at Catalent evaluated a newly developed multi-column chromatography system, the Octave BIO, that was released in September 2022 by Tosoh Bioscience.
Emily Schirmer explained the background of this project and how bioprocessing needs are changing the industry: From large pharma companies to contract manufacturers, several trends are changing the industry landscape. We are seeing higher productivity cell lines and increased use of process intensification and continuous processing methods to further drive higher productivity. These technologies and product development approaches have enabled a significant increase in the amount of material that can be generated upstream. The increase in upstream material means there is a need for efficient downstream purification methods to avoid bottlenecks and reduce manufacturing footprints.
Purification of antibody modalities
Purification platforms for monoclonal antibodies (mAbs) typically contain an affinity capture step based on protein A followed by polishing steps for further impurities reduction. Today these steps are typically performed in batch chromatography with process columns. Innovations in downstream mAb processing, including continuous chromatography approaches such as multi-column chromatography (MCC), have been shown to increase purification productivity and reduce operating costs significantly. Although batch processes are inherently less complex, MCC takes significant advantage of spreading the sample load across multiple columns in a more efficient cyclical process. As a result, a several-fold increase in productivity typically is achieved.
Multi-column chromatography
Multi-column chromatography relies on a series of small columns instead of one large column, reducing the total resin volume required by as much as 90 percent. The various operations of the process protocol (loading, washing, elution, and cleaning) are carried out simultaneously in different columns under the control of individual pumps. Periodic switching of the inlet and outlet streams to downstream column positions via a valve system enables the progression of process steps in a continuous cycle. MCC also allows maximum productivity, as mass transfer to the Protein A chromatography resin allows the total capacity of columns to be reached as fast as possible while maintaining high purity and recovery.
Some biopharma manufacturers no longer want or need to deal with the large stainless steel equipment, as well as buffer and resin volumes associated with batch processes. MCC addresses the bottlenecks that companies may experience and can provide significant economic advantages compared to traditional batch methods for mAb purification, including 310-fold increased productivity, 8595 percent resin capacity utilisation, 3050 percent reduced buffer consumption, decreased column volume, and smaller versatile process skids.
From batch to continuous
Emily stated: Catalent has been and is continuing to consider alternatives to traditional batch chromatography to address process intensification upstream. Protein A media can be costly often requiring a large upfront investment to establish the downstream process. The investment required for high-cost chromatography matrices can be limiting for biotechnology firms and can be mitigated by using MCC since smaller columns are used, which reduces resin usage. And that is how our partnership with Tosoh came about. We worked with Tosoh’s MCC systems and completed several pilot and manufacturing scale demonstration runs.
The holistic MCC solution
Octave BIO is a comprehensive and versatile multi-column chromatography system with a modular design and added functionalities that support a range of process scales, implementations, and applications, including continuous purification. Octave BIO is the first in a series of MCC instruments targeting all stages of biologic manufacturing, from pre-clinical to clinical and commercial GMP manufacturing. SkillPakTM BIO pre-packed columns are designed with standard shorter bed heights optimised for the fast flow rates and short residence times of MCC. The Octave solution consisting of the MCC instrument combined with bespoke columns enables customers to quickly and efficiently develop pre-clinical processes.
MCC affinity capturing of mAbs
TOYOPEARL® Protein A and Protein L resins provide the ideal combination of capacity, flow properties, and resulting product purity to achieve the highest productivity when used in MCC methods for the capture of antibody-based therapeutics. Octave systems paired with TOYOPEARL AF-rProtein A HC-650F resin, for example, allow flow rates of >600 cm/h and loading residence time as short as 0.25 min for Protein A adsorption of the mAb versus 4 min or more in a single column batch process. As all non-loading steps are carried out simultaneously in the other columns, there is no delay in completing each step. Protein A capture is achieved with greater speed and efficiency than a single-column process. Flexibility is afforded by adjusting the column number, size, and configuration to suit feed and adsorbent properties, accommodate all process steps, and satisfy run time requirements.
MCC expertise and training
Tosoh has been investing in the support infrastructure to help educate current and future MCC users with virtual and in-person offerings. At MCC Centers of Excellence in the U.S. headquarters in King of Prussia, PA, and in the European headquarters in Griesheim, Germany, Tosoh’s renowned chromatography experts are ready to train and support the industry from the lab to the field.
Emily Schirmer’s conclusion after the demonstration runs: The results of the in-depth MCC evaluation clearly illustrated the potential for significant time and cost savings for Catalent’s partners. The automated system also provides benefits to operating costs and time. As the industry looks to overcome the bottlenecks that can occur during intensified processes, MCC can offer a pertinent solution. Based on the positive feedback from the industry, we at Tosoh Bioscience are convinced that MCC fits the growing industry trend of switching from batch to continuous processes and meets the four design principles for biologic facilities of the future: fast, flexible, small, and sustainable.
Contact:
Regina Roemling,
Senior Marketing Communication Manager at Tosoh Bioscience GmbH
regina.roemling@tosoh.com