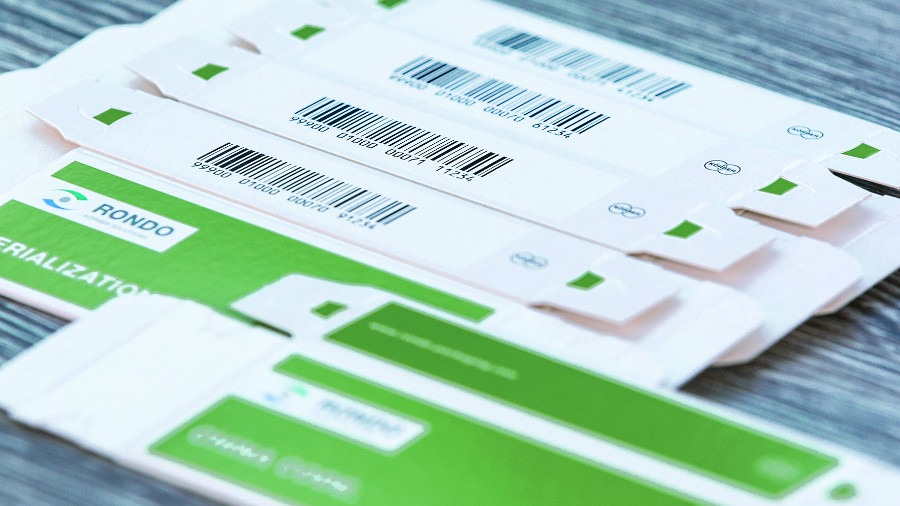
Rapid implemenation of off-line serialisation
Serialisation of drugs is confronting pharmaceutical companies all over the world with challenges, especially in relation to data handling and the integration of additional equipment and functions into existing packaging lines. Offline solutions, where secondary packaging is serialized directly by the folding-box manufacturer, combined with sophisticated data flow architectures, are a reliable, flexible, and immediately available alternative to inline serialisation.
By means of Delegated Regulation (EU) 2016/161, the European Union has drawn up a mandatory standard to prevent the penetration of falsified medicines into the legal supply chain and to increase patient protection. According to this Regulation, all prescription medicines – with the exception of those on the white list, and those medicines for self-medication cited on the black list – must be provided with an individual distinguishing feature (serialisation) and with protection from manipulation (tamper evidence).
In addition to improved patient safety, pharmaceutical manufacturers hope, through serialisation of their drugs, to contain the substantial world-wide increase in economic damage due to product piracy and theft. Apart from economic damage, manufacturers are also afraid that their brand image will be seriously damaged.
From an economic viewpoint, pharmaceutical companies can benefit from other aspects of serialisation. For example, recognisability in the event of returns and clear identifiability in the event of recalls – which can be carried out in a more targeted fashion, therefore affecting a smaller quantity of products – reduce costs substantially in some cases. Also, the grey marketing of drugs, particularly the selling of original products outside designated commercial channels, can be better controlled in this way.
Pharmaceutical companies therefore have an interest in promoting serialisation of their products. However, above all they must comply with national standards in order to be allowed to continue to supply after the respective introductory periods. Its introduction confronts pharmaceutical companies with major challenges, in particular with regard to the assignment of data to packaging lines and to the integration of serialisation equipment into existing packaging lines. In the case of retroactive integration, the pharmaceutical contractor is the general contractor, who, however, frequently does not have available the necessary technical personnel with the qualification required for this.
Challenges for manufacturers
Apart from the EU, a large number of governments throughout the world are tackling serialisation of medicines and are in the process establishing standards which differ greatly from each other. Manufacturers who wish to sell their drugs world-wide must, permanently and at short notice, get to grips with and react to new requirements, some of which may change suddenly.
Application of the codes on the individual medicine pack requires secure management within the company of the serial numbers of each individual product and, if necessary, of each individual destination country. During printing using digital print technology there is a requirement for a system at the production machine which prevents duplications, particularly in fault situations and exceptional situations, and which can reliably record the successfully printed codes despite interference factors. Because of the use of Asian fonts, the need to apply specific information to medicine packaging which people can read leads to a large quantity of characters to be processed and to exponentially demanding requirements in terms of data processing.
Outsourcing serialisation
The alternative to inline serialisation on the packaging line – offline serialisation by the folding-box manufacturer – spares the pharmaceutical company the cost of integrating printing technology, cameras, and ejection equipment into each individual packaging line, as well as training employees in the use of print technology. The lost production time for the integration and validation period can likewise be saved.
In the case of inline solutions, print heads for applying the codes with the required print quality and permanence, as well as cameras to check them and software for central control of the new modules, must be integrated into existing installations. In addition, for some countries, aggregation with balancing must be installed. The latter is also necessary for the offline variant, where serialisation is handled by the folding-box manufacturer. However, any further investment or delicate interventions in systems is not necessary, so their efficiency remains to a large extent unaffected. The basis for offline serialisation is reliable data exchange with the folding-box manufacturer.
For the EU, and for most other countries (except China), coding of the expiry date and batch information is required. Depending on the medicine, this data can subject the coding process to time pressure. If serialisation takes place at the folding-box manufacturer, then the latter must have a database system and a quality assurance system that have been proven in practice to guarantee fast, error-free deliveries.
Whether inline or offline, serialisation demands the perfect interaction of hardware, software, and reliable, qualifiable processes. Different IT systems must be combined at the equipment level (line server), production level (plant server), and as part of enterprise resource planning (ERP).
Serialisation by the folding-box manufacturer provides ultramodern printing techniques combined with reliable data flow architectures and processes which comply with pharma requirements.
The offline variant is an attractive option for medium-sized pharma companies in particular, allowing them to avoid additional investment for each individual packaging line and maintain the efficiency of existing equipment – especially if the time for converting all lines is tight. In addition to solutions for tamper evidence and the application of special security features, Rondo also offers its customers this service. The Swiss company has invested in an Atlantic Zeiser DIGILINE Single Pharma 450, which covers all the requirements for reliable offline serialisation. All current codes are applied using OMEGA Drop-on-Demand inkjet technology in high-quality, high- contrast print and codes, using UV-hardening ink, and are therefore resistant to abrasion, water, alcohol and other solvents. The legibility of bundles, which are packed in shrink foil, is significantly improved as a result, and this reduces finishing costs to a minimum. Almost all typical materials can be printed on with a print quality of at least 1.5, according to ISO/IEC 15415:2011 (Grading C).
With its extensive format range of 80 x 100 mm to 450 x 500 mm, the system handles all common sheet and cardboard sizes in the pharmaceutical industry. Up to 240 folding boxes per minute can be printed with consistent high-quality, and provided with serial numbers. In this way, Rondo is providing its customers with solutions that can also handle fairly large orders at short notice.
All modules of the coding machine, such as the mix-up and inspection cameras, are controlled via central production software. The seamlessly integrated Unique Code Software enables as many sets of numbers as required to be managed, and ensures consistent serialisation results. For example, in the event of interruptions in production, whether intended or not, no duplicate serial numbers are assigned. If desired, the list of successfully printed serial numbers can also be made available to the customer. Integration into Rondo’s existing ERP system makes duplicate inputs impossible and guarantees error-free, secure data exchange. The software has been specially adapted for Rondo, in order to enable secure management of print orders and their assignment and distribution across one or more machines for parallel production.
In addition to the software, the data flow architecture has also been adapted to the specific requirements of the pharmaceutical industry. Importing of data from the customer is also automated, as is data export of the resulting files. Assignment of serial numbers to the production order is performed using unique naming with automatically generated file names. For production, the data is provided automatically via an enhanced master data management system.
For quality assurance, a second camera that checks the correctness and quality of the codes is installed in the equipment. The production results report and the balance file can be generated in different data formats according to the customer’s wishes and sent to the customer via electronic data exchange.
Outsourcing the serialisation of their medicines to a folding-box manufacturer, such as Rondo, offers pharmaceutical manufacturers a number of benefits.
Secure offline solutions
Customers can access the very latest print technologies with high-contrast print images for optimum verifiability and secure software solutions without having to invest several times in production equipment or impair their efficiency. In addition, outsourcing serialisation does not increase the cost of line clearance during the packaging process.
With Rondo, pharma companies can rely on secure data handling and reliable balancing. Data management runs in the background and cannot be influenced by users in any of the individual process steps. Input errors are therefore prevented.
Furthermore, pharmaceutical manufacturers can access the expertise of folding-box manufacturers in terms of print, materials, and solutions. For instance, in addition to serialisation of flat cardboard blanks, Rondo also offers its customers reliable, high-quality printing of glued folding boxes, significantly reducing the quantity of serial numbers required by the process. Integration of additional security features and tamper evidence are also possible. This means that Rondo can provide its customers with both standardized and customized solutions for secure packaging which meet all international standards.
(First published in European Biotechnology, Autumn Edition 2017)