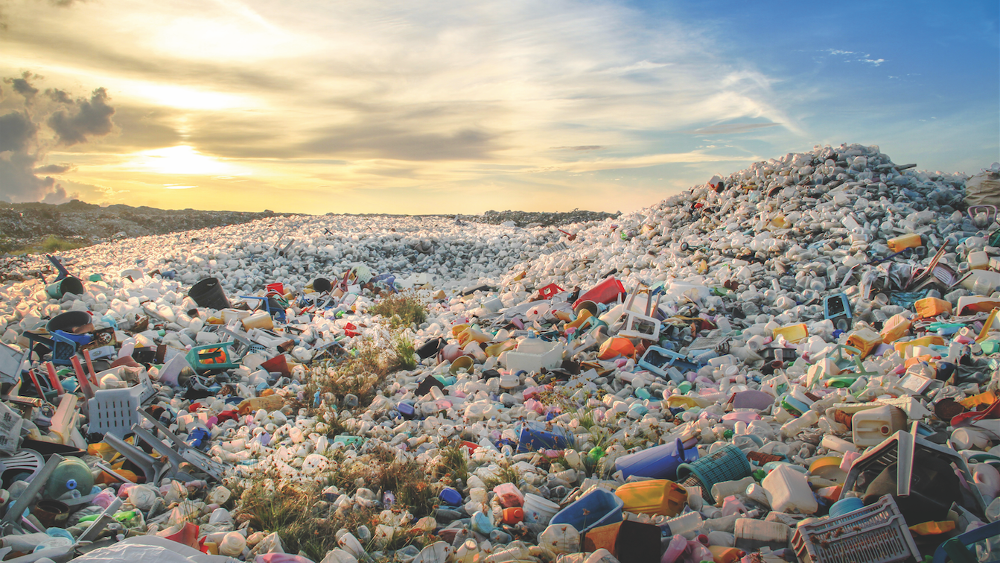
Biotech for breaking down a sea of waste
While bio-based polymers have been a hot topic for some years now, it's grown increasingly clear that where plastics end up is at least as important as how they're made. Current recycling technologies are limited, bringing either low-quality recyclates or high processing costs. But enzymes now offer a glimmer of hope. Working with the common plastic PET, a French firm is trying to prove biotech approaches can close the loop in the material's life cycle. They hope they'll soon be able to recycle the plastic endlessly and affordably.
Plastics are great materials, says Martin Stephan, they’re cheap and easy to manufacture, and they can have many different properties. Of course, the debuty CEO of French green chemistry biotech Carbios SA is also very aware that there’s a flipside to all the practicality – nearly indestructible litter. We’ve neglected the end-of-life in plastics for far too long, he adds. In a recent perspective published in Science, US researchers Jeanette Garcia and Megan Robertson found that although there are important incentives for plastics recycling, end-of-life treatment options are in practice quite limited. They estimate that energy equivalent to 3.5 billion barrels of oil – currently worth approximately US$176bn – could be saved if we recycled all the plastic solid waste on the planet. The most pressing problem is with plastic packaging materials, which make up nearly 60% of the mountain of plastic waste generated in Europe every year. Only 14% of polymer-based packaging waste is collected for recycling globally. Europe manages around 30-40%.
Closing the loop with PET
There are a number of reasons why recycling isn’t more widespread. Sorting waste is costly and time-consuming, and recycling it is energy-intensive. Available recycling technologies also work only for a few different polymers. And most importantly – the quality of recycled materials is often worse than bio-based or oil-based originals. That’s where Carbios comes in. The French company’s team of 19 claims it has developed a new technology for polyethylene terephthalate (PET) recycling that is truly circular. Stephan says the method takes care of the problem of quality loss, and believes Carbios can bring a lot of value to the PET value chain.
Roughly half of all solid plastics produced annually are used just once before ending up in the trash. That’s 150 million tonnes wasted in the truest sense of the word. PET is one of the most common and important plastics out there. It’s mainly used for synthetic fibres and bottles. Western Europe consumes around 4.3 million tonnes of PET each year, says Stephan. Estimates say around 2.7 million tonnes are not recycled, but end up in landfills or are incinerated. We believe we’re tapping a huge unused feedstock source here. He’s quick to point out that Carbios is not competing with other currently available recycling technologies: Its just another one on the list but this approach is the only one opening the path to infinite recycling.
Cracking the plastics space
What makes the Carbios process unique at this stage is that it’s based on enzymes. I think we are the first to create a new space for enzyme use, which is the plastics industry. We have the ambition to do that on a commercial scale, Stephan says. I think we’re the most advanced with our technology. And there’s no question that we are the only company with a process that’s close to market.
Enzymes in the recycling industry as a whole are not a new idea. Danish companies Novozymes and Ørsted have developed a waste-to-biogas conversion and recycling plant that relies on enzymes liquefying organic compounds in mixed-matter household wastes. There are no details about the enzyme mix as this is considered commercially sensitive information, Hannes Reuter, Head of New Bio Solutions at Ørsted told European Biotechnology. The biggest so-called Renescience plant, which will be able to process 15 tonnes of trash an hour, is getting ready to throw open its doors in Northwich (UK). Several other companies are working on biotechbased strategies for recovering metals from electronic waste, or isolating carbon fibres from discarded composite materials. But enzymes that could break down plastics at a scale that addresses the current torrent of waste? Most in the industry would just shake their heads, because petroleum-based plastics are highly resistant to enzymatic degradation. It’s true that some newly developed bio-based plastics have been designed to biodegrade’ (see box p. 56) but production scales and use of those materials are still extremely limited. In Europe, over 80% of the plastics sold today are petroleum-based: polyethylene (PE), polypropylene (PP), polystyrene (PS), polyvinyl chloride (PVC), polyurethane (PEU), and of course PET. Among them are polymers that contain a pure carbon backbone (PE, PP, PS, PVC), which are especially hard to break down into monomers. The outlook turns out to be a bit more hopeful for PET and PUR, because both of those polymers have backbones that also contain nitrogen or oxygen atoms. Some lipases, cutinases and esterases isolated from fungi or bacteria are able to depolymerise PET. Speaking to European Biotechnology, Carbios manager Stephan did not want to disclose the type(s) of enzymes his company is working with, or the organisms they are sourced from. It’s possible that the process Carbios has discovered involves several enzymes that work in parallel or sequentially. A patent published in April 2017 suggests the PET is not treated with enzymes directly, but instead with microorganisms excreting a depolymerase. The enzyme(s) in question might have been tweaked and improved in the lab as well, as recombinant versions are also covered by the patent.
It’s possible to depolymerise PET in several ways. One that likely plays a role in the company’s process degrades PET into terephthalic acid (TPA) and monoethylene glycol (MEG) very efficiently. Its a low-temperature biological process that runs at 60°-70°C, says Stephan. It depolymerises any kind of PET…the transparent one used for bottles, of course, but also the coloured version and the opaque version as well as mixed PET articles. And it also works with polyester fibres – the type of PET used for textiles.
The French Connection
In mid-2017, Carbios started scaling up the technology from laboratory to pilot plant. Within five years, the company says it hopes to be running it at the industrial scale. Support in the process is being provided by French cosmetics heavyweight L’Oréal. The two firms signed an agreement in late October to jointly establish a five-year consortium to bring Carbios’ technology to market. And the partnership remains open to companies from other industries. Our technology brings value for the recycling companies as well as the brand owners, Stephan points out. He’s convinced the Carbios model would also pay off for other consumer goods, and even non-brand industries. One of the objectives of the consortium is to create demand for the first demonstration plant to be built until 2022, he says. Members of the consortium will be prioritised when production slots are assigned.
Recycling is also a topic for emerging plastics producers. Amsterdam-based Synvina has received a preliminary OK from the European PET Bottle Platform allowing its new 100% bio-based polymer polyethylene furanoate (PEF) bottles to be fed in into the European PET bottle recycling system. The new bottles are expected to hit the market by around 2020.
Italian company Bio-On, on the other hand, is focussing on polyhydroxyalkanoates (PHA), a family of naturally occurring polymers that can be processed into hard or soft plastics, as well as into both crystalline and amorphous polymers. All of the members of the PHA family are biodegradable in industrial composting equipment, in the soil, and in both freshwater and seawater. In November, Bio-On installed two 100,000 litre fermenters at its newly built plant near Bologna – the first PHA plant in Europe. With an investment of €20m, the company’s Minerv Bio Cosmetics will produce a 100% PHA biodegradable and bio-based plastic designed to replace conventional microbeads in cosmetics. The plant will run with agricultural products such as molasses and sugar beet syrups. Other PHA companies are choosing to focus on wastewater, used cooking oil or household food waste as possible carbon sources. Although ideas like this have been around for decades, high production costs have always been an insurmountable barrier to success for these plastics. But technological breakthroughs and rising investment are now shifting the landscape. According to European Bioplastics, PHA production is set to nearly triple over the next five years.
Diversity isn’t always good
The wide variety of plastics out there on the market poses a serious problem for recyclers. In its 2017 report The New Plastics Economy, Britain’s Ellen MacArthur Foundation warned of a threat from continued, unrestrained diversification, which, while often bringing important functional benefits, have lower value in the after-use recycling system and drive up costs. The charity set up by the former solo long-distance yachtswoman sums up a problem that has dogged recyclers since the very earliest days of their industry. In the highly fragmented plastics recycling space, economies of scale are very hard to achieve. The report also demands a rise in the percentage of high-quality recyclates, which would in turn enable more high-value applications.
Currently, plastic that’s collected for recycling is mainly processed into new, low grade products that are of limited use. One example is the Fairy Ocean Plastic Bottle, which was created by consumer chemistry giant Procter & Gamble and recycling company Terracycle. Made of post-consumer recycled plastic (90%) and recycled beach and ocean plastics (10%), the bottle contains washing-up liquid. The problem with classic mechanical recycling methods is that quality deteriorates every cycle. Grinding PET waste into flakes and further regranulation will always provide a less pure recycling track than depolymerising PET into monomers. With cascaded recycling you lose quality at every step, Carbios’ Martin Stephan says. Its good, but not good enough. Our recycled PET monomers can be reused to produce so-called virgin PET.
That sounds great in theory, but will biotech recycling really prove to be viable? The French company is convinced it will. They’re already thinking about the next step. When we’ll have scaled-up our PET recycling process, we’ll move on to another polymer, says Stephan. We see a lot of potential for enzymes to depolymerise plastics.
Politics – help and hindrance
That’s a positive attitude, but Carbios and other companies at the forefront of the race to develop enzyme recycling technology still face big barriers. One major problem is that support from politics is fickle at best. When the European Parliament voted in favour of four legislative amendments in March to help the EU recycle 70% of all municipal waste and 80% of all packaging material by 2030, it received little support from the Council of the EU. European politics magazine Politico reports that the bloc’s other decisionmaking body also recently slashed a Commission recycling target for materials like plastic from 55% to 30% by 2025. Western European countries are in favour, while Eastern and Northern European countries are not. They still rely heavily on landfills or waste incineration, and lack the elaborate systems that are a prerequisite for achieving such ambitious goals. And without that infrastructure, even the most modern recycling technologies will struggle to prevail.
(First published in European Biotechnology, Winter Edition 2017)